Dr. Divya Singhal
&
Keshav Ram Singhal
Not less than nine times the term ‘statutory and regulatory requirements’ has been stated in the ISO 9001:2008 QMS Standard. This article is an attempt to understand the meaning of the term, and what and how organization needs to comply it.
The term ‘statutory and regulatory requirements’ are legal requirements as clarified in Note 2 under the clause 1.1 (General) of ISO 9001:2008 QMS Standard. This term expresses two types of requirements:
(i) Statutory requirements
(ii) Regulatory requirements
Both statutory requirements and regulatory requirements are those requirements that are required by law. These requirements are non-negotiable and must be complied with. Failure to comply a legal requirement may result in a fine or penalty and possibly a custodial sentence for the person or persons responsible for such failure. Statutory refers to laws passed by a state and/or central government, while regulatory refers to a rule issued by a regulatory body appointed by a state and/or central government.
Statutory requirements are those requirements which are applicable by virtue of law enacted by the government. A regulatory requirement can be termed as administrative legislation that constitutes or constraints rights and allocates responsibilities. It is somewhat different from the statutory legislation enacted by passing the law in the legislative assembly or parliament. There can be following types of regulations applicable on an organization:
- Legal restrictions or responsibilities promulgated by a government authority
- Self regulation by an industry through trade association
ISO 9001:2008 QMS Standard requires an organization to determine and control the statutory and regulatory requirements applicable to the organization’s products (including services). It is up to the organization how to comply this within its quality management system. On perusal of ISO 9001:2008 QMS Standard, we find, in the introduction part of the standard indicates that the standard, ISO 9001:2008 QMS, can be used by parties to assess organization’s ability to meet:
- Customer requirements
- Statutory and regulatory requirements applicable to the product
- Organization’s own requirements
So it is for the people involved in assessing the organization’s quality management system, such as third party auditors and internal auditors, need to be aware of the general and specific statutory and regulatory requirements applicable to the product within the scope of the quality management system.
The term ‘statutory and regulatory requirements’ has been used four times in clause 1 (Scope) – two times in mentioning the general scope of the standard in clause 1.1, one time in explaining the term in the note 2 under clause 1.1 and one time in mentioning the application in clause 1.2 of the standard. Accordingly, an organization, wishes to implement ISO 9001:2008 QMS Standard, needs to (i) consistently provide product that must meet applicable statutory and regulatory requirements, (ii) apply effective management system that aims to comply applicable statutory and regulatory requirements, (iii) ensure that any exclusions within clause 7 of the Standard do not affect the organization’s ability or responsibility to provide product that meets requirements.
Even in case of an outsourced process, it is the responsibility of the organization to comply statutory and regulatory requirements. This is clarified in note 3 under clause 4.1 (General requirements) of the Standard.
The Standard, in its clause 5.1 (Management commitment), has provided responsibility on the part of the top management to communicate the importance of meeting statutory and regulatory requirements and, in clause 7.2.1 (Determination of requirements related to the product), it requires the organization to determine statutory and regulatory requirements applicable to the product. Clause 7.3.2 (Design and development inputs) of the standard requires including statutory and regulatory requirements in the design input and reviewing it for adequacy.
Accordingly, the organization should have a methodology in place (i) for determining, maintaining and updating all applicable statutory and regulatory requirements, (ii) for communicating all applicable statutory and regulatory requirements within the organization. The organization should ensure that determined statutory and regulatory requirements are utilized as ‘process inputs’. The organization should monitor ‘process outputs’ for compliance with statutory and regulatory requirements.
In this regard, one suggestion could be to have a task-force team in place comprising of one In-charge and a few members, having legal knowledge or background. Task-force team should determine the applicable statutory and regulatory requirements applicable to the product and to the organization, and also ascertain the responsibility of personnel/departments in meeting these determined requirements. Task-force members may also study the national/international level best practices in this regard to gain ideas about smooth implementation of such requirements. The In-charge should ensure: communication of determined statutory and regulatory requirements to the management representative and personnel/departments concerned with a copy to the top management.
It should be the responsibility of the personnel/departments concerned to meet these determined requirements. The top management should also review at defined intervals meeting applicable statutory and regulatory requirements.
The term ‘statutory and regulatory requirements’ is invisible in clause 8 (Measurement, analysis and improvement), however internal auditors can play a significant role in meeting statutory and regulatory requirements. It will be a good idea that the auditor during the audit preparation phase obtains relevant information from internal as well as external sources with respect to the statutory and regulatory requirements that may apply to the organization and its product, such as, legal requirements related to health, safety and environment. An internal auditor can find the compliance during audit process by inquiring to the following:
- Whether the organization has determined applicable statutory and regulatory requirements related to the product?
- What are the determined applicable statutory and regulatory requirements?
- How the organization’s people are communicated the importance of meeting statutory and regulatory requirements?
- Whether the determined statutory and regulatory requirements are utilized as process inputs in determination of requirements related to the product and also in reviewing design and development inputs.
In case the auditor finds any noncompliance to any of the statutory and regulatory requirements, it should be reported as CAR (corrective action request) and such action will help the organization in improving the effectiveness of the organization’s quality management system.
An effort to create awareness .... Editor - Keshav Ram Singhal, Ajmer, India
Welcome!
Welcome!
Please also visit following blogs:
- 'ISO 9001 QMS Awareness' Blog in Hindi
- 'EMS Awareness' Blog
- 'Departmental Inquiry Awareness' Blog
- 'ISO 9001:2015 QMS Awareness' Blog
Academic comments are invited.
Encouragement Support - National Centre for Quality Management. Please become a member of NCQM.
Keshav Ram Singhal
Various information, quotes, data, figures used in this blog are the result of collection from various sources, such as newspapers, books, magazines, websites, authors, speakers etc. Unfortunately, sources are not always noted. The editor of this blog thanks all such sources.
People from more than 145 countries/economies have visited this blog: Afghanistan, Albania, Algeria, Angola, Argentina, Aruba, Australia, Austria, Azerbaijan, Bahrain, Bangladesh, Belarus, Belgium, Belize, Benin, Bhutan, Bosnia and Herzegovina, Botswana, Brazil, Brunei, Bulgaria, Burundi, Cameroon, Cambodia, Canada, Chile, China, Colombia, Costa Rica, Croatia, Cyprus, Czech Republic, Denmark, Dominican Republic, Ecuador, Egypt, El Salvador, Estonia, Ethiopia, European Union, Fiji, Finland, France, Georgia, Germany, Ghana, Gibraltar, Greece, Guatemala, Guyana, Haiti, Honduras, Hong Kong S. A. R. (China), Hungary, Iceland, India, Indonesia, Iraq, Ireland, Israel, Italy, Ivory Coast, Jamaica, Japan, Jersey, Jordan, Kazakhstan, Kenya, Kuwait, Laos, Latvia, Lebanon, Lesotho, Libya, Lithuania, Luxembourg, Macao S. A. R. (China), Macedonia, Malawi, Malaysia, Maldives, Malta, Manila, Mauritius, Mexico, Moldova, Mongolia, Montenegro, Morocco, Mozambique, Myanmar, Namibia, Nepal, Netherlands, New Zealand, Nigeria, Niue, Norway, Oman, Pakistan, Palestinian Territory, Panama, Papua New Guinea, Peru, Philippines, Poland, Portugal, Puerto Rico, Qatar, Rwanda, Romania, Russia, Saint Lucia, Samoa, Saudi Arabia, Saint Kitts and Navis, Serbia, Seychelles, Singapore, Slovakia, Slovenia, Somalia, South Africa, South Korea, Spain, Sri Lanka, Sudan, Swaziland, Sweden, Switzerland, Syria, Taiwan, Tanzania, Thailand, Trinidad and Tobago, Tunisia, Turkey, Turks and Caicos Islands, UAE, Uganda, UK, Ukraine, USA, Uzbekistan, Venezuela, Vietnam, Zambia, Zimbabwe etc. Total visitors number crossed 100,000 on 14. 02. 2013. Total visitors number crossed 145,000 on 30. 09. 2013. Total visitors > 200,000 (from 01.08.2014)
(adsbygoogle = window.adsbygoogle || []).push({});
Thursday, February 23, 2012
Tuesday, February 21, 2012
QUESTION-ANSWER FORUM
Question: It is not very clear what exactly is the difference between the process approach and system approach. Please explain.
Answer: Unfortunately, people confuse the term ‘process’ and ‘system’. It is necessary to understand both terms clearly. A process is a set of interrelated or interacting activities, which transforms inputs into outputs. The process of a business is the totality of all of the individual activities that the business performs. The process includes identifying a customer need, creating a product or service concept to meet the need, defining how that concept will be executed, executing or deploying the concept, measuring customer satisfaction, and continually improving both concepts and deployment. To manage the process, the organization develops management systems, including financial, human resources, materials, quality, environmental, health and safety, and other management systems. Some of these systems will meet the international Standards, such as ISO 9001: 2008 QMS Standard.
‘Process approach’ requires determination of processes, interactions of the determined processes and their management. In this connection, general requirements mentioned in clause 1.1 of the ISO 9001:2008 QMS Standard are relevant.
Ongoing control is one advantage of the process approach. Process approach provides over the linkage between the individual processes within the system of processes, as well as over their combination and interaction. A process approach (when used in the quality management system) emphasizes importance of:
• Understanding customer requirements, applicable statutory and regulatory requirements and organization’s own requirements
• Fulfilling customer requirements, applicable statutory and regulatory requirements and organization’s own requirements
• The need to consider processes in terms of added value
• Continual improvement of processes based on objective measurement
In each such system, there are number of component processes. The summation of these component processes constitutes the specific management system. Typical processes in the quality management system include leadership, planning, administration, purchasing, training, design and development, production and service, operations, measurement, audit, corrective and preventive actions, and improvement.
A process map is a very significant tool as part of quality management system of an organization. Part of creating this map is defining where process starts and ends and determining: the specific activities that need to be performed, the process owners for each of the activities, and customer satisfaction measures. From this map, the organization can begin to define which QMS-related processes are involved and how organization can flowchart them in detail, improve them, update the flowchart, and document, deploy and maintain the process.
I hope the matter is clear.
With best wishes,
KRS
Answer: Unfortunately, people confuse the term ‘process’ and ‘system’. It is necessary to understand both terms clearly. A process is a set of interrelated or interacting activities, which transforms inputs into outputs. The process of a business is the totality of all of the individual activities that the business performs. The process includes identifying a customer need, creating a product or service concept to meet the need, defining how that concept will be executed, executing or deploying the concept, measuring customer satisfaction, and continually improving both concepts and deployment. To manage the process, the organization develops management systems, including financial, human resources, materials, quality, environmental, health and safety, and other management systems. Some of these systems will meet the international Standards, such as ISO 9001: 2008 QMS Standard.
‘Process approach’ requires determination of processes, interactions of the determined processes and their management. In this connection, general requirements mentioned in clause 1.1 of the ISO 9001:2008 QMS Standard are relevant.
Ongoing control is one advantage of the process approach. Process approach provides over the linkage between the individual processes within the system of processes, as well as over their combination and interaction. A process approach (when used in the quality management system) emphasizes importance of:
• Understanding customer requirements, applicable statutory and regulatory requirements and organization’s own requirements
• Fulfilling customer requirements, applicable statutory and regulatory requirements and organization’s own requirements
• The need to consider processes in terms of added value
• Continual improvement of processes based on objective measurement
In each such system, there are number of component processes. The summation of these component processes constitutes the specific management system. Typical processes in the quality management system include leadership, planning, administration, purchasing, training, design and development, production and service, operations, measurement, audit, corrective and preventive actions, and improvement.
A process map is a very significant tool as part of quality management system of an organization. Part of creating this map is defining where process starts and ends and determining: the specific activities that need to be performed, the process owners for each of the activities, and customer satisfaction measures. From this map, the organization can begin to define which QMS-related processes are involved and how organization can flowchart them in detail, improve them, update the flowchart, and document, deploy and maintain the process.
I hope the matter is clear.
With best wishes,
KRS
Monday, February 20, 2012
The term 'statutory and regulatory requirements'
How many times the term 'statutory and regulatory requirements' used in ISO 9001:2008 QMS Standard?
One - Clause 0.1 (General)
Three - Clause 1.1 (Scope - General)
One - Clause 1.2 (Scope - Application)
One - Clause 4.1 (QMS - General requirements)
One - Clause 5.1 (Management commitment)
One - Clause 7.2.1 (Determination of requirements related to the product)
One - Clause 7.3.2 (Design and development inputs)
Do you find anywhere the term 'statutory and regulatory requirements' in clause 8 (Measurement, analysis and improvement) requirements?

The term 'statutory and regulatory requirements' is invisible in clause 8, however internal auditors can play a significant role in meeting statutory and regulatory requirements. It will be a good idea that the auditor during the audit preparation phase obtains relevant information from internal as well as external sources with respect to the statutory and regulatory requirements that may apply to the organization and its product, such as, legal requirements related to health, safety and environment.
In case the auditor finds any noncompliance to any of the statutory and regulatory requirements, it should be reported as CAR (corrective action request) and such action will help the organization in improving the effectiveness of the organization’s quality management system.
What is your opinion?
With best wishes,
KRS
One - Clause 0.1 (General)
Three - Clause 1.1 (Scope - General)
One - Clause 1.2 (Scope - Application)
One - Clause 4.1 (QMS - General requirements)
One - Clause 5.1 (Management commitment)
One - Clause 7.2.1 (Determination of requirements related to the product)
One - Clause 7.3.2 (Design and development inputs)
Do you find anywhere the term 'statutory and regulatory requirements' in clause 8 (Measurement, analysis and improvement) requirements?

The term 'statutory and regulatory requirements' is invisible in clause 8, however internal auditors can play a significant role in meeting statutory and regulatory requirements. It will be a good idea that the auditor during the audit preparation phase obtains relevant information from internal as well as external sources with respect to the statutory and regulatory requirements that may apply to the organization and its product, such as, legal requirements related to health, safety and environment.
In case the auditor finds any noncompliance to any of the statutory and regulatory requirements, it should be reported as CAR (corrective action request) and such action will help the organization in improving the effectiveness of the organization’s quality management system.
What is your opinion?
With best wishes,
KRS
Tuesday, February 7, 2012
STRATIFICATION
Write-up – 10
Understanding Statistical Tools and Techniques
STRATIFICATION
Stratification is a statistical tool used in combination with other analysis tool. When data from a variety of sources or categories lump together, it is difficult to visualize the meaning of data. Stratification technique separates the data so that pattern of the data can be seen.
Stratification is a technique used to analyze or divide a universe of data into homogeneous groups (strata) often data collected about a problem or event represents multiple sources that need to be treated separately. It involves looking at process data, splitting it into distinct layers (almost like a rock is stratified) and doing analysis to possibly see a process improvement. Stratification is related to segmentation, but it is different from segmentation.
Following procedure will be useful:
- Before collecting data, consider the information and sources of data that can have effect on the results. Plan to collect stratification information.
- After collecting data, when you plot or graph the collected data on scatter diagram or control chart or histogram or any other analysis tool, use different marks or colours to differentiate data from various sources.
- Data plotted or graphed that differentiate from each other are said to be stratified.
- Analyze subsets of stratified data separately.
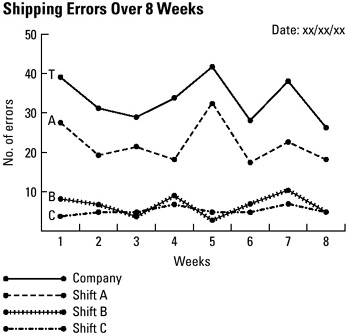
Some examples of different sources that may require data to be stratified are different equipment, shifts, departments, materials, suppliers, products, days or time.
Thus, analysis of survey data can be benefited from stratification technique.
How you liked the write-up. Please post your comments. Thanks.
Understanding Statistical Tools and Techniques
STRATIFICATION
Stratification is a statistical tool used in combination with other analysis tool. When data from a variety of sources or categories lump together, it is difficult to visualize the meaning of data. Stratification technique separates the data so that pattern of the data can be seen.
Stratification is a technique used to analyze or divide a universe of data into homogeneous groups (strata) often data collected about a problem or event represents multiple sources that need to be treated separately. It involves looking at process data, splitting it into distinct layers (almost like a rock is stratified) and doing analysis to possibly see a process improvement. Stratification is related to segmentation, but it is different from segmentation.
Following procedure will be useful:
- Before collecting data, consider the information and sources of data that can have effect on the results. Plan to collect stratification information.
- After collecting data, when you plot or graph the collected data on scatter diagram or control chart or histogram or any other analysis tool, use different marks or colours to differentiate data from various sources.
- Data plotted or graphed that differentiate from each other are said to be stratified.
- Analyze subsets of stratified data separately.
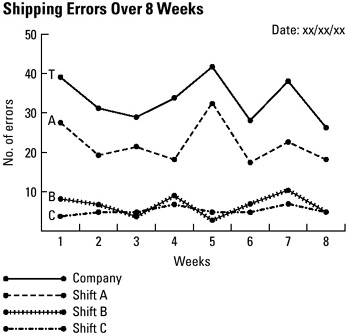
Some examples of different sources that may require data to be stratified are different equipment, shifts, departments, materials, suppliers, products, days or time.
Thus, analysis of survey data can be benefited from stratification technique.
How you liked the write-up. Please post your comments. Thanks.
Monday, February 6, 2012
SCATTER DIAGRAM
Write-up – 9
Understanding Statistical Tools and Techniques
SCATTER DIAGRAM
A scatter diagram is a graphical representation of two variables showing the relationship between them. If variables are correlated, the points will fall along a line or a curve. This diagram is also known as a scatter plot, x-y graph, or correlation chart. It is a problem solving tool.
We can use scatter diagram when we may have paired numerical data and one variable data is dependent on other variable. Scatter diagram can be constructed by plotting two variables against one another on a pair of axes. With the help of scatter diagram, we can try to determine whether two variables are related and potential root causes of problems.

It will be useful to draw scatter diagram after brainstorming causes and effects using a cause and effect diagram to determine whether a particular cause and effect are related. A scatter diagram is used to uncover possible cause-and-effect relationship.
Following procedure will be useful to construct a scatter diagram:
- Decide two variables against which you wish to see the relationship
- Collect pairs of data of these two variables
- Draw a graph with independent variable on the horizontal axis and the dependent variable on the vertical axis
- For each pair of data, put a dot or symbol where x-axis value intersect y-axis value
- Look at the pattern of dots (or symbols) to see if a relationship is obvious
- If data form a line or a curve, it indicates that variables are correlated

When data forms a line or curve, then you may use regression analysis or correlation analysis by using following steps:
- Decide the points from top to bottom by drawing horizontal line
- Divide the points from left to right by drawing a vertical line
- If number of points is odd, you should draw the line through the middle point
- In this way, you will be able to divide points on the graph into four quadrants
- Count the points in each quadrant (leaving the point on the line)
- Add diagonally opposite quadrants
- Find smaller sum and total of points in all quadrants
- A = points in upper left + points in lower right
- B = points in upper right + points in lower left
- Q = the smaller of A and B
- N = A + B
- Look up the limit for N on the trend test table

- If Q is less than the limit, two variables are related
- If q is greater than or equal to the limit, the pattern could have occurred from random chance and we can say that no relationship is demonstrated
How you liked the write-up. Please post your comments. Thanks.
Understanding Statistical Tools and Techniques
SCATTER DIAGRAM
A scatter diagram is a graphical representation of two variables showing the relationship between them. If variables are correlated, the points will fall along a line or a curve. This diagram is also known as a scatter plot, x-y graph, or correlation chart. It is a problem solving tool.
We can use scatter diagram when we may have paired numerical data and one variable data is dependent on other variable. Scatter diagram can be constructed by plotting two variables against one another on a pair of axes. With the help of scatter diagram, we can try to determine whether two variables are related and potential root causes of problems.

It will be useful to draw scatter diagram after brainstorming causes and effects using a cause and effect diagram to determine whether a particular cause and effect are related. A scatter diagram is used to uncover possible cause-and-effect relationship.
Following procedure will be useful to construct a scatter diagram:
- Decide two variables against which you wish to see the relationship
- Collect pairs of data of these two variables
- Draw a graph with independent variable on the horizontal axis and the dependent variable on the vertical axis
- For each pair of data, put a dot or symbol where x-axis value intersect y-axis value
- Look at the pattern of dots (or symbols) to see if a relationship is obvious
- If data form a line or a curve, it indicates that variables are correlated

When data forms a line or curve, then you may use regression analysis or correlation analysis by using following steps:
- Decide the points from top to bottom by drawing horizontal line
- Divide the points from left to right by drawing a vertical line
- If number of points is odd, you should draw the line through the middle point
- In this way, you will be able to divide points on the graph into four quadrants
- Count the points in each quadrant (leaving the point on the line)
- Add diagonally opposite quadrants
- Find smaller sum and total of points in all quadrants
- A = points in upper left + points in lower right
- B = points in upper right + points in lower left
- Q = the smaller of A and B
- N = A + B
- Look up the limit for N on the trend test table

- If Q is less than the limit, two variables are related
- If q is greater than or equal to the limit, the pattern could have occurred from random chance and we can say that no relationship is demonstrated
How you liked the write-up. Please post your comments. Thanks.
Thursday, February 2, 2012
PARETO CHART
Write-up – 8
Understanding Statistical Tools and Techniques
PARETO CHART
A pareto chart looks like a bar graph, but it contains both bars and a line graph. It is one of the basic tools of quality control. The length of the bars in the graph represents frequency or cost (time or money). These bars are arranged with longest bar on the left and shortest to the right. This is a tool which can be used to analyze the ideas from brainstorming session. This tool is also known as Pareto diagram or Pareto analysis. This tool is used to identify the vital few problems or causes of problems that have the greatest impact on the process. This chart pictorially represents data in the form of a ranked bar chart that shows the frequency of occurrence of items in descending order. The Pareto chart is named after Wilfried Fritz Pareto, an Italian engineer, sociologist, economist, political scientist and philosopher. He introduced the concept of Pareto efficiency.

It is significant to use Pareto chart:
- To analyze data about frequency of problems or causes of problems in a process
- To focus on the most significant problem or cause, when there are many problems or causes
- To analyze broad causes
- To communicate with others about the data

Following procedure will be useful to use Pareto chart and its analysis:
- Decide the categories of group items
- Decide approximate measurement (frequency, quantity, cost, or time)
- Decide the time period to gather data and use in the Pareto chart (one work cycle, one full day, or one week)
- Collect data, record and assemble data for the category each time
- Subtotal the measurements for each category
- Determine the appropriate scale for the measurements data collected
- Mark the scale on the left side of the chart
- Construct and label bars for each category by placing the tallest to the left, next tallest to its right and so on
- Calculate the percentage for each category
- Draw a right vertical axis and label it with percentage in a graph paper. Be sure that left measurement corresponds to one-half and it should be exactly opposite 50% on the right scale.
- Calculate and draw cumulative sums
- Add the subtotals for the first category and second category and place a dot above the second bar indicating the sum, then add subtotal of third category to the sum and place a dot above the third bar indicating the new sum and so on. Continue the adding subtotals and placing dots for all bars.
- Connect the dots, starting from the top of first bar. The last dot should reach 100 percent on the right side
In this way we can visualize the most important factors among a typically large set of factors through the Pareto chart. A Pareto chart often represents the most common sources of defects, the highest occurring type of defect, or the most frequent reasons for problems.
How you liked the write-up. Please post your comments. Thanks.
Understanding Statistical Tools and Techniques
PARETO CHART
A pareto chart looks like a bar graph, but it contains both bars and a line graph. It is one of the basic tools of quality control. The length of the bars in the graph represents frequency or cost (time or money). These bars are arranged with longest bar on the left and shortest to the right. This is a tool which can be used to analyze the ideas from brainstorming session. This tool is also known as Pareto diagram or Pareto analysis. This tool is used to identify the vital few problems or causes of problems that have the greatest impact on the process. This chart pictorially represents data in the form of a ranked bar chart that shows the frequency of occurrence of items in descending order. The Pareto chart is named after Wilfried Fritz Pareto, an Italian engineer, sociologist, economist, political scientist and philosopher. He introduced the concept of Pareto efficiency.

It is significant to use Pareto chart:
- To analyze data about frequency of problems or causes of problems in a process
- To focus on the most significant problem or cause, when there are many problems or causes
- To analyze broad causes
- To communicate with others about the data

Following procedure will be useful to use Pareto chart and its analysis:
- Decide the categories of group items
- Decide approximate measurement (frequency, quantity, cost, or time)
- Decide the time period to gather data and use in the Pareto chart (one work cycle, one full day, or one week)
- Collect data, record and assemble data for the category each time
- Subtotal the measurements for each category
- Determine the appropriate scale for the measurements data collected
- Mark the scale on the left side of the chart
- Construct and label bars for each category by placing the tallest to the left, next tallest to its right and so on
- Calculate the percentage for each category
- Draw a right vertical axis and label it with percentage in a graph paper. Be sure that left measurement corresponds to one-half and it should be exactly opposite 50% on the right scale.
- Calculate and draw cumulative sums
- Add the subtotals for the first category and second category and place a dot above the second bar indicating the sum, then add subtotal of third category to the sum and place a dot above the third bar indicating the new sum and so on. Continue the adding subtotals and placing dots for all bars.
- Connect the dots, starting from the top of first bar. The last dot should reach 100 percent on the right side
In this way we can visualize the most important factors among a typically large set of factors through the Pareto chart. A Pareto chart often represents the most common sources of defects, the highest occurring type of defect, or the most frequent reasons for problems.
How you liked the write-up. Please post your comments. Thanks.
Wednesday, February 1, 2012
HISTOGRAM
Write-up – 7
Understanding Statistical Tools and Techniques
HISTOGRAM
A histogram is a snapshot of variation or distribution, where data are grouped into cells and their frequency represented as bars. It is a commonly used graph to show frequency distribution. It looks like a bar chart, but it is different from the bar chart. We can put the data from the check sheets into a histogram. A histogram is a set of vertical bars whose areas are proportional to the frequency represented.
The histogram helps in analyzing the capability of a process. The variables being measured are shown along x-axis and the frequency occurrences of each measurement is charted along y-axis.
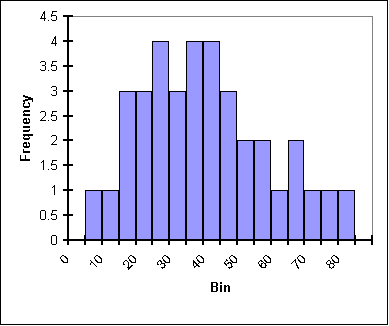
A histogram is convenient for large amounts of data particularly when the range is wide. It gives a picture of the extent of variation. It highlights unusual areas and indicates probability of particular values occurring. Histogram depicts the central tendency or mean of the data and its variation or spread.
A histogram is useful in showing characteristics of the process being measured, such as:
- Whether results of the process show a normal distribution – a bell curve?
- Whether the range of the data indicates that the process is capable of producing product as per defined specifications?
- How much improvement is necessary to meet specifications?
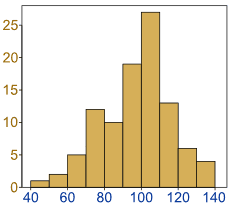
It is convenient to use histogram when data are numerical and we want to see the shape of data distribution to determine whether the output of a process shows normal distribution.
Following procedure will be useful:
- Decide a process to observe
- Collect at least 50 consecutive data points from the process
- Use histogram worksheet to set up histogram
- Draw x- and y-axes on the graph paper. Y-axes should be used mark and label for counting data values (frequency values) and x-axis to mark and label with variable values from the histogram worksheet.
For using histogram, we need to use histogram worksheet to set up the histogram on graph paper. Histogram worksheet helps in determining the number of bars, the range of numbers that go into each bar and labels for the bar edge.
How you liked the write-up. Please post your comments. Thanks.
Understanding Statistical Tools and Techniques
HISTOGRAM
A histogram is a snapshot of variation or distribution, where data are grouped into cells and their frequency represented as bars. It is a commonly used graph to show frequency distribution. It looks like a bar chart, but it is different from the bar chart. We can put the data from the check sheets into a histogram. A histogram is a set of vertical bars whose areas are proportional to the frequency represented.
The histogram helps in analyzing the capability of a process. The variables being measured are shown along x-axis and the frequency occurrences of each measurement is charted along y-axis.
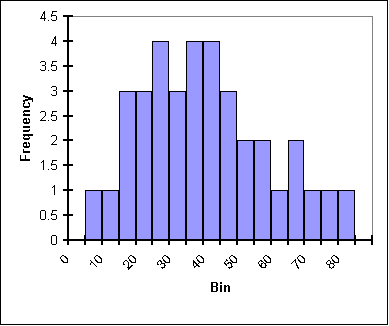
A histogram is convenient for large amounts of data particularly when the range is wide. It gives a picture of the extent of variation. It highlights unusual areas and indicates probability of particular values occurring. Histogram depicts the central tendency or mean of the data and its variation or spread.
A histogram is useful in showing characteristics of the process being measured, such as:
- Whether results of the process show a normal distribution – a bell curve?
- Whether the range of the data indicates that the process is capable of producing product as per defined specifications?
- How much improvement is necessary to meet specifications?
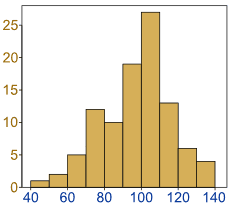
It is convenient to use histogram when data are numerical and we want to see the shape of data distribution to determine whether the output of a process shows normal distribution.
Following procedure will be useful:
- Decide a process to observe
- Collect at least 50 consecutive data points from the process
- Use histogram worksheet to set up histogram
- Draw x- and y-axes on the graph paper. Y-axes should be used mark and label for counting data values (frequency values) and x-axis to mark and label with variable values from the histogram worksheet.
For using histogram, we need to use histogram worksheet to set up the histogram on graph paper. Histogram worksheet helps in determining the number of bars, the range of numbers that go into each bar and labels for the bar edge.
How you liked the write-up. Please post your comments. Thanks.
CONTROL CHART
Write-up – 6
Understanding Statistical Tools and Techniques
CONTROL CHART
One of the key tools of Statistical Process Control (SPC) is a control chart. It is used to study and monitor a repetitive process, so that the process may remain in control.
Organizations use interrelated processes resulting output as a product. The outcome of a process is never exactly the same every time. Fluctuation or variability is an inevitable component of all processes or systems and it is expected. Fluctuation or variability arises naturally from the effects of miscellaneous chance events. If outcome of a process remains within the stable pattern, then we can say that the process is OK, but variation outside a stable pattern may be an indication that the process is not OK in a consistent manner. Event or outcome, finally beyond expected variability indicates that the process is out of control.
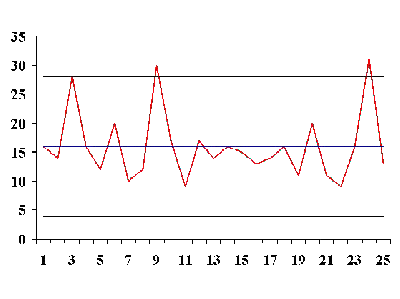
The control chart is a graph, which is used to show how a process changes over time. Data are plotted in time order. A control chart for a process has the following lines:
- A central line for the average
- An upper line for the upper control limit
- A lower line for the lower control limit
The values for the central line, upper line and lower line (i.e. control limits) are determined from historic data. These can be determined by computation based upon (i) the data covering past and current process records, (ii) statistical formulae whose reliability has been proved in practice. By comparing current data to these lines in the graph, one can come to the conclusion whether the process is in control or out of control. There are various types of control charts, divided in two groups – (i) Control chart for variables, and (ii) Control chart for attributes.

A control chart can be used:
- To control ongoing process by finding and correcting problems as they occur
- To predict the expected range of outcome from a process
- To determine whether a process is stable
- To analyze patterns of a process variations from special causes or common causes
- To determine whether improvement initiatives should aim to prevent specific problem or make changes to the process
Following procedure will be useful:
- Select the process that you wish to study, monitor or control
- Define the process control chart with average central line, upper control limit line and lower control limit line
- Determine the appropriate time period for collecting and plotting data
- Collect data and construct the control chart graph by plotting the data on the chart
- Analyze the graph, identify those signals which are ‘out-of-control’ on the chart and mark them on the graph
- Investigate the cause
- Document investigation process mentioning how investigated, what are the causes, what needs to be done to correct the ‘out-f-control’ situation
Standard control limits are located at 3-sigma away from the average or central line of the chart, known as 3-sigma limits. Control limits define a zone where observed data for a stable and consistent process occurs virtually all the time – 99.7%. Any fluctuations within these limits come from the common causes inherent to the process. Any fluctuations beyond the control limits results from a special cause that require fundamental change or improvement in the process. Any fluctuations beyond the control limits show that the process is out-of-control. When fluctuations are noticed beyond control limits then it is required to investigate and eliminate the special cause. Thus control chart can be used as a quality-monitoring tool.
How you liked the write-up. Please post your comments. Thanks.
Understanding Statistical Tools and Techniques
CONTROL CHART
One of the key tools of Statistical Process Control (SPC) is a control chart. It is used to study and monitor a repetitive process, so that the process may remain in control.
Organizations use interrelated processes resulting output as a product. The outcome of a process is never exactly the same every time. Fluctuation or variability is an inevitable component of all processes or systems and it is expected. Fluctuation or variability arises naturally from the effects of miscellaneous chance events. If outcome of a process remains within the stable pattern, then we can say that the process is OK, but variation outside a stable pattern may be an indication that the process is not OK in a consistent manner. Event or outcome, finally beyond expected variability indicates that the process is out of control.
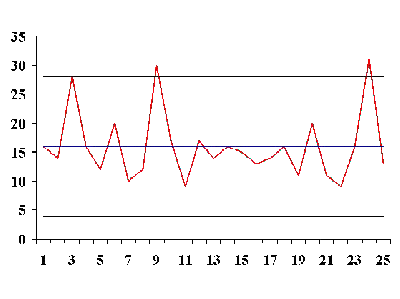
The control chart is a graph, which is used to show how a process changes over time. Data are plotted in time order. A control chart for a process has the following lines:
- A central line for the average
- An upper line for the upper control limit
- A lower line for the lower control limit
The values for the central line, upper line and lower line (i.e. control limits) are determined from historic data. These can be determined by computation based upon (i) the data covering past and current process records, (ii) statistical formulae whose reliability has been proved in practice. By comparing current data to these lines in the graph, one can come to the conclusion whether the process is in control or out of control. There are various types of control charts, divided in two groups – (i) Control chart for variables, and (ii) Control chart for attributes.

A control chart can be used:
- To control ongoing process by finding and correcting problems as they occur
- To predict the expected range of outcome from a process
- To determine whether a process is stable
- To analyze patterns of a process variations from special causes or common causes
- To determine whether improvement initiatives should aim to prevent specific problem or make changes to the process
Following procedure will be useful:
- Select the process that you wish to study, monitor or control
- Define the process control chart with average central line, upper control limit line and lower control limit line
- Determine the appropriate time period for collecting and plotting data
- Collect data and construct the control chart graph by plotting the data on the chart
- Analyze the graph, identify those signals which are ‘out-of-control’ on the chart and mark them on the graph
- Investigate the cause
- Document investigation process mentioning how investigated, what are the causes, what needs to be done to correct the ‘out-f-control’ situation
Standard control limits are located at 3-sigma away from the average or central line of the chart, known as 3-sigma limits. Control limits define a zone where observed data for a stable and consistent process occurs virtually all the time – 99.7%. Any fluctuations within these limits come from the common causes inherent to the process. Any fluctuations beyond the control limits results from a special cause that require fundamental change or improvement in the process. Any fluctuations beyond the control limits show that the process is out-of-control. When fluctuations are noticed beyond control limits then it is required to investigate and eliminate the special cause. Thus control chart can be used as a quality-monitoring tool.
How you liked the write-up. Please post your comments. Thanks.
Subscribe to:
Posts (Atom)